Split seals sealing technology Renault engineers
Split seals sealing technology Renault engineers Installing split seals will eliminate sleeve wear and associated maintenance interventions and costs, and can eliminate the need for packing adjustments as well as packing gland leakage and associated cleanup costs. Most split mechanical seals are designed to seal outside of the stuffing box Split seals sealing technology Renault engineers.
The Benefits of Split Seals
In split mechanical seals, all the parts are split into at least two halves.
Like traditional nonsplit mechanical seals, they are applied on rotating equipment, such as pumps, mixers and agitators. Like other mechanical seals, they seal the interface of the rotating shaft and the equipment housing. Being split, the seals can be installed around the shaft as opposed to being slid onto the shaft during equipment assembly.
Split mechanical seals were first used to seal submarine main propulsion shafts back in 1954.
It was some time later, around 1986, when split seals were introduced to the process industries as a standard, off-the-shelf available rotating shaft sealing technology.
Since the first-generation split seal was introduced, many technological improvements have been made and integrated into the latest generation of split seals.
These improvements have greatly expanded the window of operation and application of split seals.
The current generation of split mechanical seals is comparable in performance to cartridge-type mechanical seals. The newest split mechanical seals are self-aligning and installed by simply fastening subassembly halves together around the shaft and bolting to the equipment. The need for measurements and accurate setting of the split components by the installer now happens automatically within these modern designs.
Split mechanical seals are available for shaft diameters from 1 inch (25 millimeters [mm]) up to 36 inches (915 mm), and with the capability to seal pressures from slight vacuum to 450 pounds per square inch (psi) (31 Bar), there are many available applications.
The materials of construction are where some limitations may apply when comparing split mechanical seals to cartridge seals.
Most noticeable is that the elastomers, which are often custom moldings, are typically only offered in fluoroelastomer (FKM), ethylene propylene diene monomer (EPDM) and tetrafluoroethylene propylene (FEPM). Face materials are typically limited to carbon and variants thereof, along with silicon carbides.
The toughness and density of tungsten carbide makes it a great choice for arduous duties but a poor choice for split seals due to the splitting methods and the rotational mass separating the split components during rotation.
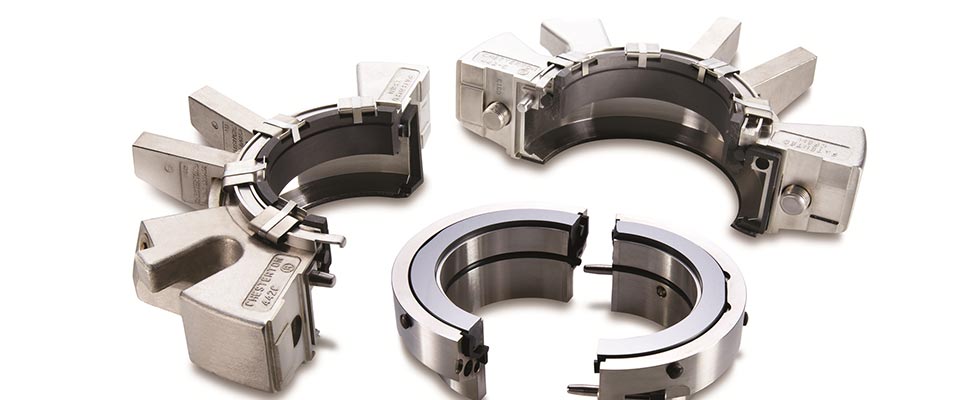
Leakage is often a concern for operators considering split seals. It should be noted that properly installed and applied split seals are known to operate leak-free for more than 10 years. The splitting of mechanical seals into halves generates a multitude of leak paths within the seal that are sealed by static secondary sealing elements. As such, there is a greater risk of static joint leakage and, as a result, split mechanical seals are not recommended for hazardous services.
Over the years, there have been various opinions regarding the startup leakage phenomena of split seals, wherein the seal may leak at up to 1 drop/shaft millimeters per minute (mm/min) for the initial 48 to 72 operating hours, as a general guide. This initial leakage typically subsides or stops completely beyond 200 hours as the split components go through various cycles of temperature, pressure and vibration.